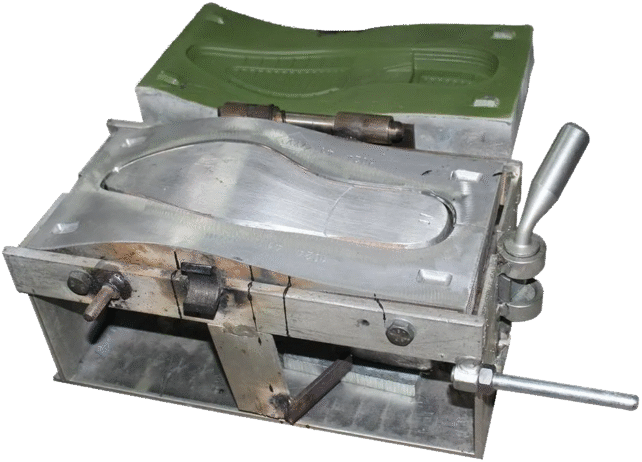
A specialized instrument used in the production of polyurethane (PU) slippers. It is designed to shape and form slipper soles and uppers through an injection or pouring process. These moulds are typically made from aluminum to ensuring durability and precision.
Important features:
- Material: High-quality aluminum or steel
- Design: Create different slipper styles and sizes.
- Process: Used in PU injection or pouring machines for mass production
- Durability: Resistant to wear and tear, ensuring consistent production quality.
- Minimum Order: Quantity 1 pair
Introduction Die PU Mould Slipper
Founded in 1990, Vats Die Makers specializes in manufacturing, trading, and wholesaling PU sole moulds, TPR sole moulds, PVC footwear moulds, and more
PU Slipper Mould Die: An Essential Tool for Footwear Manufacturing
The PU slipper mould die is a important component in the footwear industry, particularly in the production of polyurethane (PU) slippers. These are made from tough materials like aluminum or steel, so that’s way its stay long and durable. Its manufacturers create slippers that fit well and feel comfortable, with lots of options for different styles, sizes, and textures. Thanks to these moulds, you get slippers that look good and feel great on your feet.
PU Slipper Mould Die
Single colour moulds – Made for creating slippers in a single colour.
Multi colour moulds – Making slippers with multiple colors or patterns.
Manual moulds – Require manual operation for PU material pouring and demoulding.
Automatic moulds – Integrated with automatic ejection systems for mass production.
High-quality aluminum or alloy materials are commonly use, For mould die design. Aluminum is use because it’s lightweight and easy to handle, while steel is selected for its strength and ability to withstand wear and tear.
The Process of PU Slipper Moulds dies Manufacturing
Designing the Mould – The mould is created based on the required slipper design and specifications.
Mould Preparation – Cleaning up to stop for sticking.
Injection or Pouring of PU Material – The liquid polyurethane is injected and poured into the mould cavity.
Heating and Curing – The material is heated and left for solidify.
Cooling and Demoulding – Once the slippers take shape, they are cooled and carefully removed from the mould.
Finishing Touches – Trim, paint, and do a final check to make sure the slippers are up to standard
Benefits of PU Slipper Mould Dies
High Precision – Produces slippers with consistent quality and design.
Durability – Long-lasting materials ensure extended use.
Mass Production – Perfect for large-scale manufacturing.
Customization – Ability to choose different size , colour, and texture
Cost effective –It helps to save materials and keeps costs down.
Maintenance
Taking good care of PU slipper mould dies is key to making sure they last and keep performing at their best. Regular cleaning, lubrication, and check-ups help stop damage and keep the moulds working well. Also, protects them from rust and wear over time.
In the footwear industry, PU slipper mould dies are very important. They make it possible to produce high-quality slippers efficiently, helping manufacturers keep up with the demand for shoes that are not only stylish but also comfortable and affordable.Proper care of these moulds helps companies use them for a longer time and make the most of their investment. That’s why regular maintenance is required for any footwear production facility.
Why PU Slipper Mould Die
A PU slipper mould die is a important tool to use in manufacturing to create the sole and upper part of PU slippers. These moulds are designed with complex detailing to achieve the required shape, pattern, and style. The production process involves injecting or pouring liquid polyurethane into the mould cavity, where it solidifies into the desired slipper form.